In industrial production, compressed air is an indispensable power source for many enterprises. However, air compressors generate a large amount of heat energy during operation, most of which is usually wasted and discharged into the atmosphere. With the continuous improvement of energy conservation and environmental protection requirements, how to effectively utilize these "waste heat" has become an important issue for enterprises to reduce energy costs. The emergence of waste heat recovery devices for air compressors provides an effective solution to this problem.
During operation, an air compressor compresses air through mechanical energy to achieve higher pressure. However, the process of air compression is not efficient, as a large amount of electrical energy is converted into thermal energy. Normally, over 80% of the input energy of an air compressor is converted into heat energy, with only a small portion used for compressing the actual power of the air, and the remaining majority of the heat being wasted through cooling systems or direct discharge.
This not only means huge energy waste, but also leads to thermal pollution of the environment. In today's world where energy costs continue to rise, how to utilize this waste heat has become the key to energy conservation and emission reduction for enterprises.
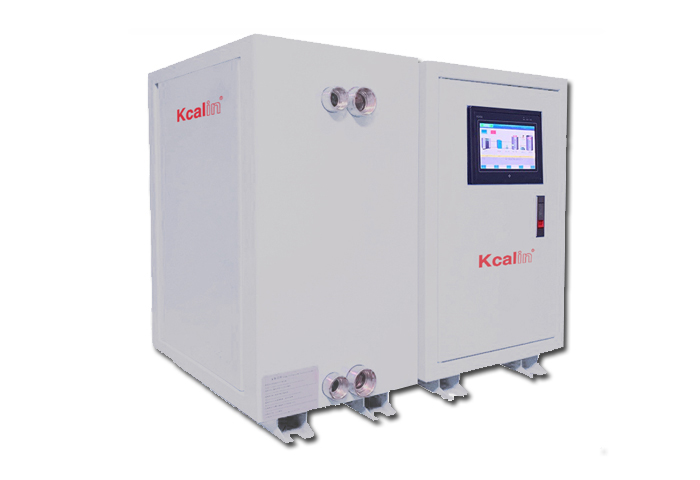
The waste heat recovery device of the air compressor transfers the heat from the high-temperature oil and gas mixture or cooling water discharged by the air compressor to other media that need to be heated, such as the hot water system, heating system or production process water in the factory. The recovered heat can be used to provide hot water for office or living areas in the factory area, or directly used for heating processes in industrial production.
Specifically, waste heat recovery devices generally include components such as heat exchangers, circulation pumps, and control systems. The heat exchanger is responsible for exchanging the heat generated by the air compressor with the refrigerant (water or oil), while the circulation pump is responsible for delivering the heat medium to the required heating equipment. The control system ensures the automated operation and efficient regulation of the entire recycling process.
By installing waste heat recovery devices, enterprises can convert the previously wasted heat energy into usable heat sources, thereby reducing the demand for external energy. This not only reduces the energy costs of enterprises, but also reduces thermal pollution to the environment, achieving a win-win situation of economic and environmental benefits.
Reduce energy costs: In most industrial enterprises, hot water, heating, and process heating are the main energy consuming links. By using air compressor waste heat recovery devices, enterprises can reduce their dependence on traditional fuels such as natural gas, coal, or electricity, significantly reducing the costs of hot water and heating. According to the actual application situation, the investment payback period of the air compressor waste heat recovery device is usually within 1-2 years, which means that the subsequent energy-saving benefits belong to the enterprise.
Improving energy utilization efficiency: The waste heat recovery device of the air compressor improves the energy utilization efficiency of the entire air compression system by converting waste heat into usable thermal energy. This improvement is not only reflected in reducing energy consumption, but also in reducing the demand for cooling systems, further reducing operating costs.
Extend equipment lifespan: The waste heat recovery device can reduce the exhaust temperature of the air compressor, thereby reducing the burden on the cooling system. The reduction of cooling system pressure helps to reduce equipment wear, extend equipment lifespan, and lower maintenance and replacement costs.
Environmental benefits: By reducing energy consumption, the air compressor waste heat recovery device can also reduce greenhouse gas emissions such as carbon dioxide and sulfides, helping companies comply with environmental regulations. This not only helps to enhance the corporate social responsibility image, but may also apply for energy-saving subsidies or tax incentives.
In the current context of energy scarcity and increasingly strict environmental requirements, enterprises must adopt more efficient energy utilization strategies. The air compressor waste heat recovery device provides a practical and feasible solution for enterprises. By effectively utilizing the waste heat generated by compressed air, it can not only significantly reduce energy costs, but also extend equipment life, reduce environmental pollution, and achieve a dual improvement of economic and environmental benefits.
For enterprises looking for new ways to save energy and reduce consumption, the air compressor waste heat recovery device is undoubtedly an efficient energy-saving tool worth considering. Through scientific design and rational application, this technology will help enterprises gain an advantage in fierce market competition and move towards a more sustainable development path.
Comment