Mines are a field full of challenges and opportunities, constantly seeking to improve efficiency, reduce costs, and reduce dependence on external energy, while also focusing on environmental protection and sustainability. In this context, the waste heat recovery technology for exhaust air has emerged as a solution for the mining industry, achieving multiple benefits from wellhead antifreeze to building heating.
In mining production, the problem of lack of air has always existed. The depth of the mine and the unique nature of the underground working environment lead to this problem, which typically manifests as the following challenges:
Worker health risks: Lack of wind reduces the supply of fresh air and poses a threat to workers' health, especially in deep mines.
Waste heat waste: Under exhaust conditions, a large amount of high-temperature heat energy is contained in the exhaust gas. However, this heat is usually wasted because there is no effective way to capture and utilize it.
The exhaust heat recovery technology is used to capture and effectively utilize the high-temperature heat energy in the exhaust gas. These thermal energy can be applied in various fields such as wellhead antifreeze, building heating, and hot water supply, bringing many potential advantages:
Energy recovery: The waste heat of exhaust air can be effectively converted into energy, reducing dependence on external energy and thus reducing energy costs.
Reducing greenhouse gas emissions: By effectively recovering heat energy from high-temperature exhaust gases, the mining industry can reduce greenhouse gas emissions and contribute to environmental protection.
Improving the worker environment: The application of heating systems improves the working environment of workers, increases job satisfaction, and helps to improve production efficiency.
The exhaust heat recovery heating system is a comprehensive engineering system aimed at capturing and effectively utilizing high-temperature heat energy in exhaust gas. The following is the basic working principle of the system:
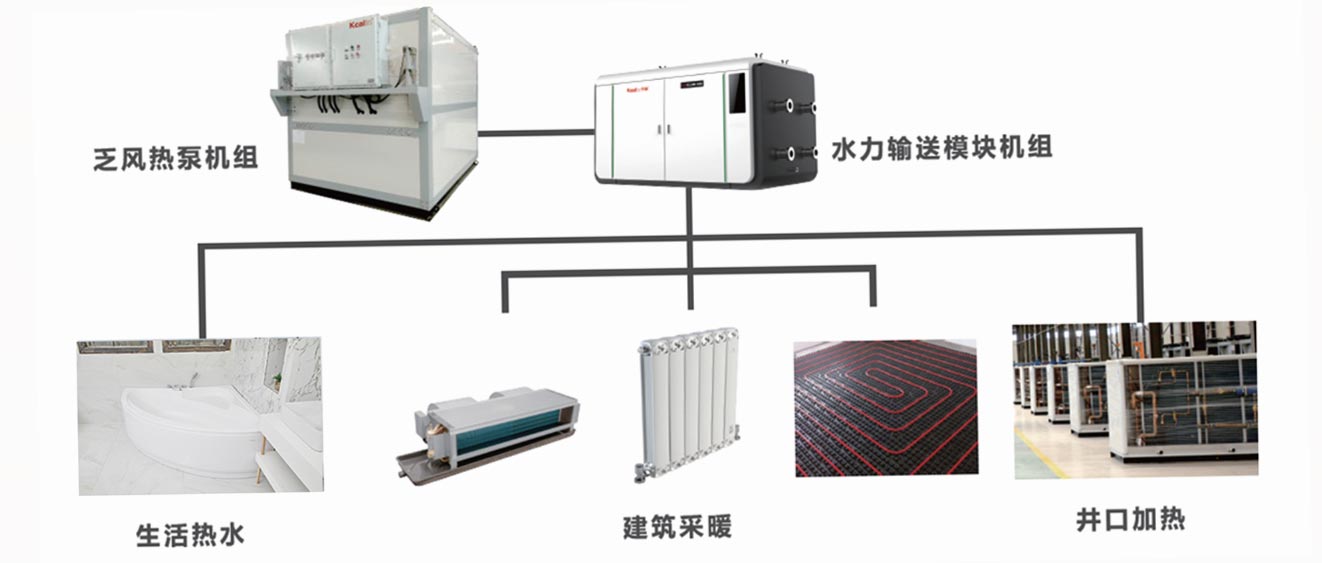
Exhaust gas recovery: The system captures the high-temperature heat in the exhaust gas through the exhaust gas collection device, usually using a heat exchanger or exhaust gas pipeline.
Heat pump technology: Waste heat is introduced into the exhaust air heat pump system, where thermal energy is transferred to the heat transfer medium used for heating, such as water or air.
Heat distribution: Through pipelines and radiators, the system distributes heat energy to various areas in mining facilities, heating buildings, or providing hot water.
Control system: The system is usually equipped with an intelligent control system to monitor temperature and energy demand to ensure the efficient operation of the heating system.
Solutions for wellhead antifreeze and building heating
Frost prevention at the wellhead: In deep mines, the wellhead area usually faces low temperatures, which may lead to equipment freezing and work interruption. The exhaust heat recovery heating system can provide sufficient heat energy for antifreeze equipment and ensure the smooth operation of the wellhead. This not only helps improve work efficiency, but also reduces maintenance and repair costs.
Building heating: Buildings within the mining site, such as office buildings, dormitories, and facilities, also require heating. Traditional heating systems typically rely on external energy sources, while exhaust heat recovery heating systems provide a more cost-effective and environmentally friendly heating option for these buildings. By distributing the captured high-temperature heat inside the building, these systems provide workers with a warm working and living environment.
The use of exhaust heat recovery heating systems brings multiple advantages, including:
Energy cost savings: By reducing reliance on external energy, mines can reduce heating costs and improve energy efficiency.
Reducing greenhouse gas emissions: Effective energy recovery can help reduce greenhouse gas emissions from mines, reduce environmental footprint, and promote sustainable development.
Improving workers' quality of life: Providing heating and hot water improves workers' comfort and quality of life, thereby helping to attract and retain talent.
Resource sustainability: The waste heat recovery and heating system of exhaust air can help improve resource sustainability, reduce environmental risks in mines, and create a more sustainable working environment for the future.
The exhaust heat recovery technology represents an innovative solution that provides multiple benefits to the mining industry, from wellhead antifreeze to building heating. It brings multiple benefits to the mining industry, including improved energy efficiency, cost savings, reduced greenhouse gas emissions, and improved workers' quality of life. The application of this technology not only helps to improve the sustainability of mines, but also helps to meet the growing energy demand while reducing dependence on external energy. In the mining industry, waste heat recovery technology for exhaust air has become an important step towards achieving sustainability and innovation.
Comment