Coal mine underground operations are a high-risk industry with complex underground environments, facing various potential hazards such as gas explosions, water permeability, roof caving, and fires. In order to ensure the safety of underground workers, coal mining enterprises must adopt a series of strict safety measures.
Gas explosion is one of the serious safety hazards in underground coal mine operations. Gas prevention and control measures mainly include:
Gas detection: Install gas detectors in the underground operation area to monitor gas concentration in real time. Once the gas concentration exceeds the safety standard, the system will automatically alarm and take corresponding emergency measures.
Ventilation management: By improving the ventilation system, ensure underground air circulation and dilute gas concentration. The ventilation system includes the main ventilation fan, auxiliary ventilation fan, and local ventilation equipment to ensure the ventilation needs of different work areas.
Gas drainage: In high gas coal seams, pre drainage gas technology is used to extract gas from the coal seam in advance, reduce underground gas concentration, and improve safety. The gas drainage system includes gas drilling, drainage pipelines, and drainage equipment.
Gas control: For areas with high gas concentration, gas control measures such as gas sealing and gas control grouting are taken to prevent gas from spreading to the working area.
Ventilation is an important guarantee measure for underground operations in coal mines. A good ventilation system can dilute harmful gases and provide fresh air. Ventilation management measures include:
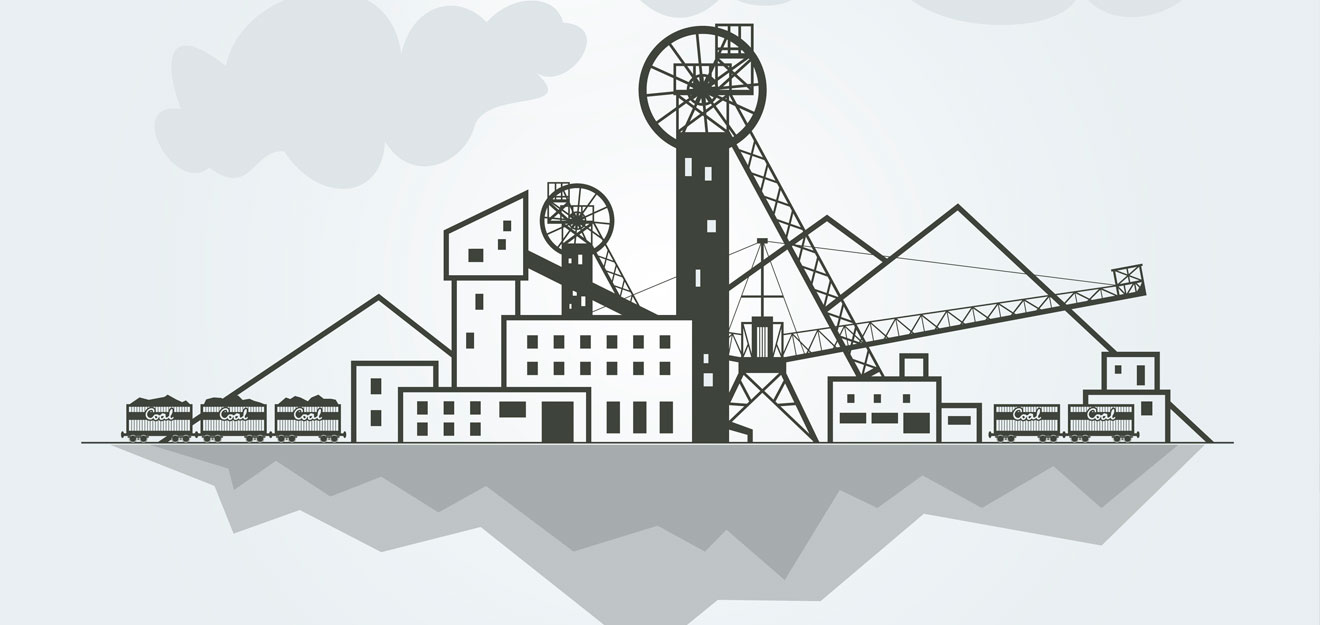
Main ventilation system: The main ventilation system consists of a main ventilation fan, air door, air bridge, etc., ensuring the ventilation of the main underground tunnels. The operation status of the main ventilation fan needs to be regularly checked to ensure its normal operation.
Auxiliary ventilation system: The auxiliary ventilation system is used to assist the main ventilation system, providing ventilation for local areas, especially in mining and excavation working faces. The auxiliary ventilation fan needs to be adjusted according to actual needs to ensure air circulation in local areas.
Local ventilation equipment: In some special work areas, such as areas with high gas concentration or poor air circulation, install local ventilation equipment, such as local ventilation fans and air ducts, to ensure the ventilation effect of the area.
Ventilation management system: Develop a comprehensive ventilation management system, clarify the operation and maintenance requirements of ventilation equipment, conduct regular ventilation inspections and evaluations, and ensure the effectiveness of the ventilation system.
Roof caving is another major danger in underground coal mining operations. The main measures for roof support include:
Support design: Design a reasonable roof support plan based on the geological conditions of different coal seams. The commonly used support methods include anchor rod support, anchor cable support, steel frame support, and concrete support.
Support construction: Strictly follow the support design scheme in the mining and excavation working faces to ensure the quality of support materials and the standardization of construction technology.
Support monitoring: Regularly monitor the effectiveness of support and promptly address any issues found. Support monitoring includes the settlement of the roof, deformation of the support structure, etc., to ensure the stability of the support system.
Dynamic support: For the risk of roof caving during the mining process, dynamic support measures such as increased support, strengthened support, and local support are taken to ensure operational safety.
Underground fires are a major safety hazard in coal mining operations, and fire prevention and control measures mainly include:
Fire source control: Strictly control underground fire sources, prohibit open flame operations, and ensure the explosion-proof performance of electrical equipment. Strictly manage flammable materials and gases to prevent fires from occurring.
Fireproof equipment: Fireproof equipment such as fire extinguishers, fire sand, and fire hoses should be equipped in the underground operation area. Regularly check the integrity and effectiveness of fire protection equipment to ensure its availability at all times.
Fire monitoring: In areas prone to fire, install fire monitoring equipment such as fire detectors and temperature sensors to monitor fire hazards in real time. Once a fire occurs, immediately report to the police and initiate firefighting measures.
Emergency plan: Develop a comprehensive fire emergency plan, conduct regular fire drills, and improve the fire emergency response capabilities of underground operators. Clarify the escape routes and measures in the event of a fire to ensure personnel safety.
Personal protection is an important measure to ensure the safety of underground workers, mainly including:
Safety helmets and shoes: Underground operators must wear safety helmets and shoes that meet the standards to prevent roof caving and foot injuries.
Respiratory protection: In areas with high gas concentration or poor air circulation, operators must wear respiratory protection equipment, such as gas masks and oxygen respirators, to prevent harmful gases from harming the human body.
Lighting equipment: The underground working environment is dim, and operators must be equipped with reliable lighting equipment, such as mining lamps and headlights, to ensure the lighting effect of the working area.
Protective clothing and gloves: Operators wear corresponding protective clothing and gloves according to different job requirements, such as fire-resistant clothing, acid and alkali resistant clothing, and wear-resistant gloves, to protect their bodies and hands from injury.
Safety training: Regularly provide safety training to underground operators to enhance their safety awareness and emergency response capabilities. The training content includes gas prevention and control, ventilation management, roof support, fire prevention and control, and personal protection, ensuring that operators master necessary safety knowledge and skills.
The working environment underground in coal mines is complex and poses various potential hazards. Ensuring the safety of workers is an important responsibility of coal mining enterprises. By adopting a series of safety measures such as gas prevention and control, ventilation management, roof support, fire prevention and control, and personal protection, the safety risks of underground operations can be effectively reduced, and the safety guarantee of operators can be improved. Coal mining enterprises should continuously improve their safety management system, enhance their safety technology level, ensure the safety and stability of underground operations, and safeguard the safety of miners.
Comment