The exhaust air waste heat recovery heat pump system is a system that utilizes the high-temperature waste heat generated in industrial production processes for energy recovery and reuse. It uses heat pump technology to transfer the heat energy from the exhaust gas to higher temperature hot water or steam to meet other processes or heating needs. The following is a detailed explanation of the application principle of the system:
Waste gas collection: The system first collects the high-temperature waste gas generated from industrial production equipment through pipelines or pipeline networks. These exhaust gases can be hot gas emissions from combustion furnaces, chimneys, or other process equipment.
Pre treatment: Waste gas usually contains pollutants such as solid particles, dust, and acidic gases, so pre treatment is required before entering the heat pump system. Common pre-treatment methods include filtration, dust removal, and desulfurization to ensure that the exhaust gas has no negative impact on the normal operation of the system.
Heat pump cycle process: After the exhaust gas enters the heat pump system, it is circulated through a series of heat exchangers, compressors, and other components. The system usually adopts a refrigerant cycle, including components such as evaporator, compressor, condenser, and expansion valve. These components work together to absorb the heat energy in the exhaust gas from a lower temperature environment and transfer it to a high-temperature thermal medium through compression and condensation processes.
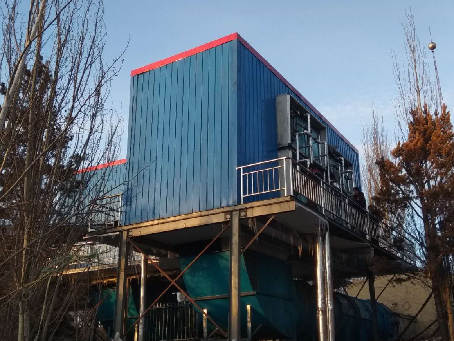
Heat exchange: During the cycling process, the heat pump system utilizes the heat energy in the exhaust gas to transfer it to the target medium, such as water or steam, through a heat exchanger. After the heat of the exhaust gas is absorbed, the temperature of the exhaust gas decreases, further improving the thermal efficiency of the system.
Thermal energy utilization: High temperature thermal media (such as hot water or steam) can be used to meet the thermal needs of other process processes, such as heating, hot water supply, or other thermal energy utilization aspects. In this way, the system achieves effective recovery and reuse of thermal energy in exhaust gas, reducing dependence on traditional energy.
Control and monitoring: In order to ensure the efficient operation of the system, heat pump recovery systems are usually equipped with automatic control systems and monitoring equipment. These devices can monitor parameters such as exhaust gas temperature, pressure, and flow in real-time, and automatically adjust the operating status of the heat pump system according to the set control strategy. By precise control and monitoring, the energy efficiency and performance of the system can be greatly improved.
The application principle of the exhaust heat recovery heat pump system can be summarized as the following key steps:
Waste gas collection: Collect high-temperature waste gas generated in industrial production.
Pre treatment: Treatment of exhaust gas, such as dust removal and desulfurization, to purify the exhaust gas and protect the heat pump system.
Heat pump cycle process: The heat pump cycle is carried out through components such as a heat exchanger and compressor, transferring the heat energy from the exhaust gas to the thermal medium.
Heat exchange: The heat energy in the exhaust gas is transferred to the target medium, such as hot water or steam, through a heat exchanger.
Thermal energy utilization: Utilizing high-temperature thermal media to meet other process or heating needs.
Control and monitoring: Real time monitoring of system parameters through automatic control and monitoring equipment, and adjustment of system operation status based on control strategies.
The application of exhaust air waste heat recovery heat pump system can be widely used in various industrial fields, such as steel, chemical industry, power, etc. It can greatly recover and utilize the heat energy in exhaust gas, reduce energy consumption, reduce negative impacts on the environment, and improve the energy efficiency performance of industrial production processes.
Comment